ISO 13485:2016 is an international quality management standard for the medical industry that establishes requirements for quality management systems in organizations involved in the production and supply of goods. medical equipment supply.
ISO 13485:2016 provides a framework of reference for the development, implementation and maintenance of an effective quality management system that ensures safety and effectiveness in the manufacture of medical products.
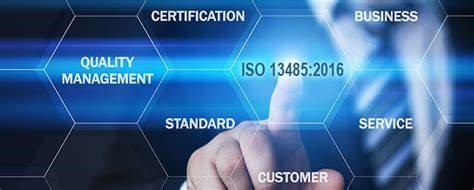
One of the key advantages of ISO 13485:2016 is that it enhances the reliability of medical products. This standard sets forth stringent requirements for controlling production processes, managing risks and ensuring compliance with health-related legislation. By complying with these requirements, an organization can provide high-quality medical products and services that strengthen the trust of customers and partners. Another point worth noting is that ISO 13485:2016 facilitates access to international markets. By complying with this standard, medical organizations can demonstrate their ability to comply with international quality regulations and procedures. This can help expand business scope, enhance competition and create opportunities to export medical products to international markets.
WE SUPPORT YOU ISO 13485: 2016
1. Gap Assessment
We offer this service to organizations that have existing documents including policies, procedures, manuals, forms, handbooks, etc. and would like to check if the existing documents meet the requirements of the desired standards and what they need to do to certify the system.
2.System Development
We offer this service to organizations that do not have any existing system (documents) including policies, procedures, manuals, forms, handbooks, etc. or the gap assessment shows that their existing system needs to improve to meet the requirements of the desired standard.
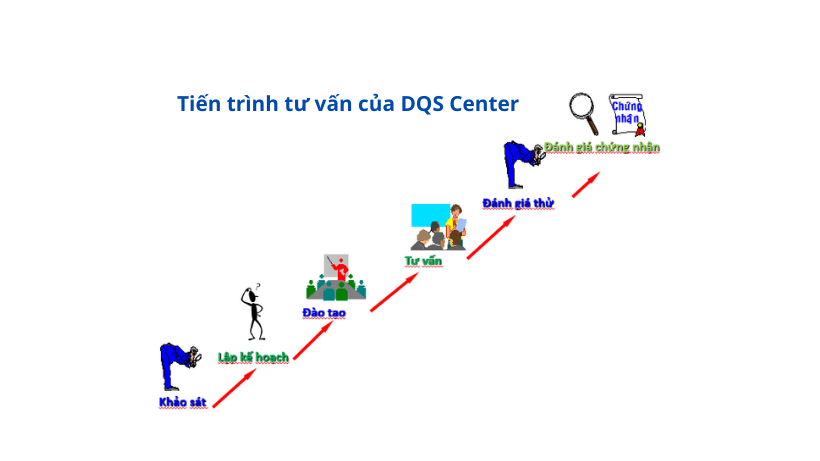
3.Implementation 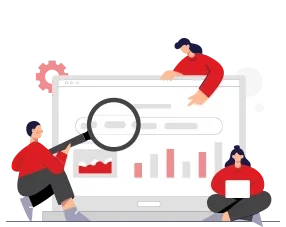
A Management system should be documented and implemented to meet the requirements of the desired standards. We will supervise and guide our clients during the Implementation of the management while they follow the policies and procedures and use the forms.
4.Internal Audit 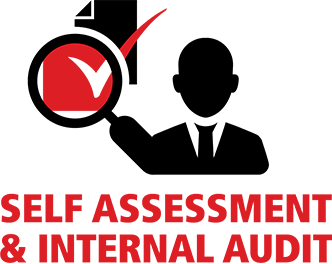
An annual internal audit is required to get certified and maintain the ISO certificates. We offer this service to organizations that do not have the internal resources to conduct the internal audits or would like to have a new pair of eyes to detect the opportunities for improvement
5. Attending External Audit 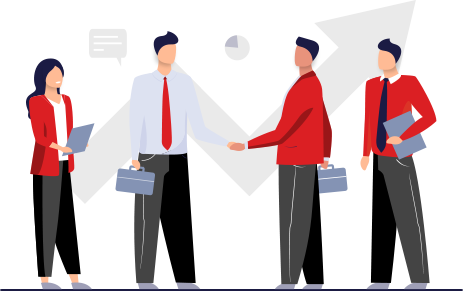
Dealing with the external auditor might be quite stressful and challenging for the organizations, particularly for the ones that are willing to certify their system for the first time. We will attend the external audit and assist them as a facilitator for a better and smoother experience.
6. Ongoing Maintenance
Once the organizations achieve their certificate, they will face a new challenge for maintaining what they have achieved as every year the certification body comes back for a surveillance audit. We offer this service to draw their attention to what they might miss in the routines.
Get a quote for ISO 13485 certification, contact us by phone number 08 1275 3919 or email at dqscenter@gmail.com
DQS Center understands the problems of enterprises in Setting and applying advanced management systems. DQS Center accompanies businesses to improve product quality. If you need advice on ISO 13485 certification, please contact DQS Center (DQSC) for the fastest support.
Contact us to start your certification process
Hotline: 08 1275 3919
Email: dqscenter@gmail.com
DQS CENTER CO., LTD
Address: No. 617, Nguyen Dinh Chieu Street, Ward 2, District 3, HCMC
ISO13485: 2016 TRAINING & CONSULTING PLAN
No. |
Items of ISO project
|
In charge |
Progress with milestone (month/ week) |
Total Man-days |
|||||||||||||||||||||||
1st month |
2nd month |
3rd month |
4th month |
5th month |
6th month |
||||||||||||||||||||||
1 |
2 |
3 |
4 |
1 |
2 |
3 |
4 |
1 |
2 |
3 |
4 |
1 |
2 |
3 |
4 |
1 |
2 |
3 |
4 |
1 |
2 |
3 |
4 |
||||
1 |
Factory tour & general documents & records survey |
Consultant & ISO team |
|
|
|
|
|
|
|
|
|
|
|
|
|
|
|
|
|
|
|
|
|
|
|
|
1 |
2 |
ISO 13485 awareness & interpretation training |
Consultant & ISO team |
|
|
|
|
|
|
|
|
|
|
|
|
|
|
|
|
|
|
|
|
|
|
|
|
2 |
3 |
Writing documents assignment for each of the Depts |
ISO team |
|
|
|
|
|
|
|
|
|
|
|
|
|
|
|
|
|
|
|
|
|
|
|
|
1 |
4 |
Writing/ modification the procedures/ documents |
Consultant & ISO team |
|
|
|
|
|
|
|
|
|
|
|
|
|
|
|
|
|
|
|
|
|
|
|
|
4 |
5 |
Issue documents |
ISO team |
|
|
|
|
|
|
|
|
|
|
|
|
|
|
|
|
|
|
|
|
|
|
|
|
– |
6 |
Training general requirements to ISO team |
Consultant & ISO team |
|
|
|
|
|
|
|
|
|
|
|
|
|
|
|
|
|
|
|
|
|
|
|
|
1 |
7 |
ISO 13485 internal auditor training |
Consultant & ISO team |
|
|
|
|
|
|
|
|
|
|
|
|
|
|
|
|
|
|
|
|
|
|
|
|
2 |
8 |
Internal audit |
Consultant & ISO team |
|
|
|
|
|
|
|
|
|
|
|
|
|
|
|
|
|
|
|
|
|
|
|
|
4 |
9 |
Management review |
BOD & ISO team |
|
|
|
|
|
|
|
|
|
|
|
|
|
|
|
|
|
|
|
|
|
|
|
|
– |
10 |
Corrective action after internal audit |
Consultant & ISO team |
|
|
|
|
|
|
|
|
|
|
|
|
|
|
|
|
|
|
|
|
|
|
|
|
1 |
11 |
Pre-audit by consultant |
Consultant & ISO team |
|
|
|
|
|
|
|
|
|
|
|
|
|
|
|
|
|
|
|
|
|
|
|
|
1 |
12 |
Certificating audit – 1st stage audit (*) |
ISO team & auditors team |
|
|
|
|
|
|
|
|
|
|
|
|
|
|
|
|
|
|
|
|
|
|
|
|
– |
13 |
Corrective action |
Consultant & ISO team |
|
|
|
|
|
|
|
|
|
|
|
|
|
|
|
|
|
|
|
|
|
|
|
|
– |
14 |
Certificating audit – 2nd stage audit (**) |
ISO team & auditors team |
|
|
|
|
|
|
|
|
|
|
|
|
|
|
|
|
|
|
|
|
|
|
|
|
– |
15 |
Total man-days |
|
|
|
|
|
|
|
17 |
Notes: Certification audit is carried out by the independent Certification Body (Ex: SGS, TUV, BV…)
LIST OF DOCUMENTS NEED TO BE WRITTEN ACCORDING TO ISO 13485: 2016
No.
|
Document’s name
|
ISO 13485 Clause
|
1
|
Quality policy |
5.3
|
2
|
Quality objective |
5.4.1
|
3
|
Quality manual |
4.2.2
|
4
|
Control of Law & compliance relating to products procedure |
1.0
|
5
|
Setting up medical equipment data & records procedure |
4.2.3 |
6
|
Control of documents procedure |
4.2.4
|
7
|
Control of records procedure |
4.2.5
|
8
|
Job description |
5.5.1
|
9
|
Communication procedure |
5.5.3 |
10
|
Management review procedure |
5.6
|
11
|
Provision of human resources procedure |
6.1
|
12
|
Competence training and management procedure |
6.2
|
13
|
Maintenance and repair procedure |
6.3
|
14
|
Mold management procedure |
6.3 |
15
|
Employees health care procedure |
6.4
|
16
|
Control of pest procedure |
6.4
|
17
|
Work environment management procedure |
6.4
|
18
|
Control of contamination procedure |
6.4.2 |
19
|
Hazard identification and risk assessment procedure |
7.1
|
20
|
Technology procedure |
7.1 |
21
|
Product standards |
7.1 |
22
|
Material standards |
7.1
|
23
|
Review of contracts procedure |
7.2
|
24
|
Evaluation of suppliers procedure |
7.4.1
|
25
|
Purchase procedure |
7.4.2
|
26
|
Material check procedure |
7.4.3
|
27
|
Control of manufacture procedure |
7.5.1
|
28
|
Control of 4M changes procedure |
7.5.1
|
29
|
Delivery procedure |
7.5.4
|
30
|
Validation of the value of using production & using software procedure |
7.5.6
|
31
|
Customer properties management procedure |
7.5.10 |
32
|
Product traceability procedure |
7.5.9 |
33
|
Samples of materials & finished products management procedure |
7.5.11 |
34
|
Input – output control procedure |
7.5.11
|
35
|
Control of measuring instrument procedure |
7.6
|
36
|
Customer feedback and complaints solving procedure |
8.2.2
|
37
|
Reporting to management agencies procedure |
8.2.4 |
38
|
Internal audit procedure |
8.2.4
|
39
|
In-process & final check procedures |
8.2.6
|
40
|
Control of nonconforming product procedure |
8.3
|
41
|
Statistic procedure (Data analysis) |
8.4
|
42
|
Improvement procedure |
8.5
|
43
|
Corrective action procedure |
8.5.2
|
44
|
Preventive action procedure |
8.5.3
|
45
|
Work instructions |
7.5.1
|